Mecaplan tehostaa AM-osaamistaan yhteistyössä Oulun yliopiston ja Nivalan Teollisuuskylä Oy:n kanssa
Mecaplan Oy on tuotekehityksen ja teknisen suunnittelun palveluyritys. Toimintamme perustuu vankkaan kokemukseen, teknisen tuotannon tietotaitoon ja asiakkaidemme tarpeiden tunnistamiseen.
Yhteistyö FMT-tutkimusryhmän kanssa materiaalia lisäävän valmistuksen (AM) tutkimuksen parissa täydentää tietotaitoamme ja parantaa kykyämme palvella asiakkaitamme heidän haasteissaan. Tulevaisuuden tuotantoteknologiat (FMT) ‑tutkimusryhmä on osa Oulun yliopiston Kerttu Saalasti ‑instituuttia. AM-tutkimusta tehdään huippuluokan 3D-metallitulostimella ELME Studiossa, Nivalan Teollisuuskylän pyörittämässä TKI-infrastruktuurissa.
Me3Lab tekninen raportti – DFAM-suunnittelu
Esittelemme tässä yhden Oulun yliopiston tekemistä tutkimuksista. Tutkimuksen tarkoituksena on havainnollistaa DFAM-prosessia (AM-suunnittelu, Design for Additive Manufacturing). DFAM on hyvä perusta uusien AM-tekniikan suunnittelumahdollisuuksien pohtimiselle. Nyrkkisääntö on, ettei materiaalia lisäävää valmistusta tulisi (useimmissa tapauksissa) käyttää, mikäli osat voidaan valmistaa perinteisillä menetelmillä. Tähän sääntöön on kuitenkin ollut joitakin poikkeuksia. Suunnitteluvaihe on AM-osien kohdalla varsin kriittinen. DFAM pitää sisällään useita erilaisia menetelmiä, kuten topologian optimointi, useiden osien yhdistäminen yhdeksi kokoonpanoksi, monimateriaalisuunnittelu, hilarakenteet jne. Tässä raportissa käsittelemme topologian optimointia ja osien yhteensovittamista. Raportti on tehty Me3Lab-nimisessä projektissa yhteistyössä C3TS-projektin kanssa.
-Tero Jokelainen
Lisätietoa Mecaplanista, projekteista ja yhteistyöstä:
- mecaplan.fi
- www.oulu.fi/fmt/
- www.nivalanteollisuuskyla.fi
- www.elmestudio.fi/fi/
- www.eura2014.fi/rrtiepa/projekti.php?projektikoodi=A71640
- www.nivalanteollisuuskyla.fi/fi/metallien-3d-valmistuslaboratorion-kaynnistaminen-me3lab/
- c3ts.eu/
DFAM ja DFMA yleisesti
DFAM (Design for Additive Manufacturing) tarkoittaa, että osat suunnitellaan erityisesti materiaalia lisäävän valmistuksen teknologiaa varten. Yleisesti tämä tarkoittaa, että osat voidaan tuottaa kannattavasti AM-tekniikalla, jos ne on suunniteltu teknologiaa varten. Seikkoja kuten useiden osien sovittaminen yhdeksi ja erilaisten ominaisuuksien tekeminen suorituskyvyn parantamiseksi, joita ei voida tehdä perinteisillä valmistus menetelmillä (jyrsintä, sorvaus, valaminen, ruiskuvalu), jne.
Yleisesti käytettyjä suunnittelumenetelmiä ovat topologian optimointi, hilarakenteiden suunnittelu ja osien yhdistäminen, ottaen lisäksi huomioon osien asemointi ja tukirakenteet. Suunnittelussa ensimmäinen vaihe on tutkia osan toiminnallisia puolia ja sitten tulostusasemointia. Seuraava vaihe on tehdä osasta 3D-tulostettava (viipalointi ja laitteen parametrien säätäminen).
DFMA-prosessia (Design For Manufacturing and Assembly) käytetään tavallisesti alentamaan tuotekehitysvaiheen kustannuksia. Kuvassa 1 näkyy DFMA-prosessin periaate. DFMA-prosessissa tuote suunnitellaan ottaen huomioon sekä kokoonpano (DFA) että tuotanto (DFM). Ensiksi tehdään konsepti, josta iterointiprosessi alkaa. Osan/kokoonpanon yksinkertaistuksia ja iterointeja jatketaan, kunnes rakenne on hyväksyttävällä tasolla. Seuraava vaihe on optimoida materiaalikustannukset valitsemalla paras materiaali, jolla on vaaditut ominaisuudet (tuotteen ominaisuudet on tunnettava!). Kun ensimmäinen iteraatiokierros on saatu valmiiksi, alkaa DFM-vaihe. Tässä vaiheessa valitaan tuotantomenetelmät sekä hienosäädetään kustannuslaskelmat ja rakennetaan prototyyppi.

Havainnollistus 1; Topologian optimoitu kiinnitinrunko
Versio 1
Kyseessä on havainnollistusosa, joka on erityisesti suunniteltu DFAM:n suunnittelumenetelmien (topologian optimointi) konkretisoimiseksi. Osan suunnittelussa oli eräitä alkuehtoja:
- Kiinnitin on automaatiolinjaa varten (tilavaraus)
- Voimat ja rajoitteet on otettava huomioon suunniteltaessa
- Osoitetut kiinnitys- ja kuormapisteet
- Ensimmäinen tavoite oli vähentää painoa eli nostaa hyötykuormaa
Kappaletta käytetään havainnollistukseen myös C3TS-projektissa (Arctic Platform to Create, 3D-print, Test and Sell). Materiaaliksi valikoitui AlSi10Mg (alumiini) alhaisen kuormituksen ja keveyden vuoksi. Eräs toinen raportti osoitti, että AlSi10Mg:n vetolujuus on 250 MPa tulostettuna ja 150 MPa päästöhehkutuksen jälkeen. (Näytekappaleet tulostettiin pystysuunnassa).
Kevyen osan suunnitteluprosessi 3D-tulostusta varten (topologian optimoinnin menetelmä):
- Liitospinnat, geometriset tilarajoitteet ja tekniset vaatimukset
- “massamalli” – 3D-malli, jossa on kuormitustilanteet, liitospinnat ja geometriset tilarajoitteet
- Alustavan 3D-geometrian muodostaminen
- Lopullisen geometrian suunnittelu
- Geometrian pääominaisuudet kerätään topologian optimoinnin tuloksista.
- Tuotantomenetelmä otetaan huomioon lopullisen geometrian suunnittelussa
- Lujuusvaatimukset otetaan huomioon tekemällä lopullinen FE-analyysi
- 3D-tulostus
Massamalli
Ensiksi suunniteltiin massamalli. Siihen sisällytettiin tilarajoitteet, ja suunnitelma täytti myös muut tekniset vaatimukset. Massamalli rajoitteineen näkyy kuvassa 2. Käytetyt reunaehdot olivat 1) kiinteät tuet yläosassa, 2) 200 N kuorma pinnalla (merkitty sinisellä kuvassa 2) ja 3) vastavoimat massamallin takana oleville rei’ille (100 N kukin).

Topologian optimoinnin tulos
Optimoinnin tavoitteena oli keventää tätä massamallia 75% kuormitusten ollessa alle 250 MPa. Optimointi alkoi kuvassa 3 näkyvällä karkealla topologian optimoinnilla. Topologian optimointi näytti, kuinka jännitykset jakautuvat rakenteessa, ja mitkä ovat tärkeimmät lopullisessa geometriassa käytettävät piirteet.

Lopullisen geometrian suunnittelu
Seuraavassa vaiheessa tehdään uudelleen suunnittelu alustavan optimoinnin tuloksien perusteella. Kuvassa 4 näkyy topologian optimoitu osa muutosten jälkeen. Lopullisen osan geometria on samankaltainen kuin karkeassa mallissa. Tähän geometriaan sisältyy myös uusia pinnanmuotoja ja pyöristyksiä verrattuna karkeaan malliin.

Muutosten jälkeen luotiin lopullinen FEM-malli ja laskettiin sekä analysoitiin kuormitukset ja siirtymät (kuva 5). FEM-tarkastelu osoitti, että osa kestää kuormitukset. Suurimmat jännitykset ja siirtymät olivat 81 MPa ja 0.1 mm. Tuloksista ilmenee, ettei suuria paikallisia kuormia ole, eli kuorma jakautuu tasaisesti kappaleeseen.
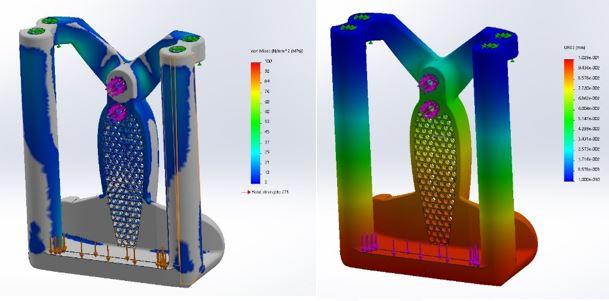
3D-tulostus
Kappaleen kokonaistilavuus oli 0.033 dm3 ja tukien tilavuus 0.005 dm3. Kuvassa 6 näkyvät tulostuskulma ja kappaleen tukirakenteet. Määritettyjen toleranssien (kiinnityspisteet ja kuormapinta) saavuttamiseksi ja pinnankarheusvaatimusten täyttämiseksi valittiin tulostuskulmaksi 30 ° ja kerrospaksuudeksi 30 µm. Tuet asetettiin pinnoille, joilta ne on helppo irrottaa. Joitain vikoja ilmeni tulostuksessa johtuen tukirakenteen virheistä. Käytännössä tietyt alueet eivät olleet kunnolla tuettuja, ja tulostus epäonnistui tukien puuttumisen vuoksi. Lisäksi tukirakenteen hampaat olivat liian heikkoja pitämään pintaa suorassa, mistä aiheutui taipumista ja osittaista romahdusta. Tulostusaika oli 8 tuntia ja 30 minuuttia yhdelle osalle ja 16 tuntia ja 30 minuuttia neljälle osalle, jolloin vastaavat kustannukset ovat noin 680 € (80 €/h * 8.5h) ja 1320 € (80 €/h * 16.5 h). Yhden osan kustannukset vähenivät 680€:sta 330€:on, kun neljä osaa tulostettiin samanaikaisesti.
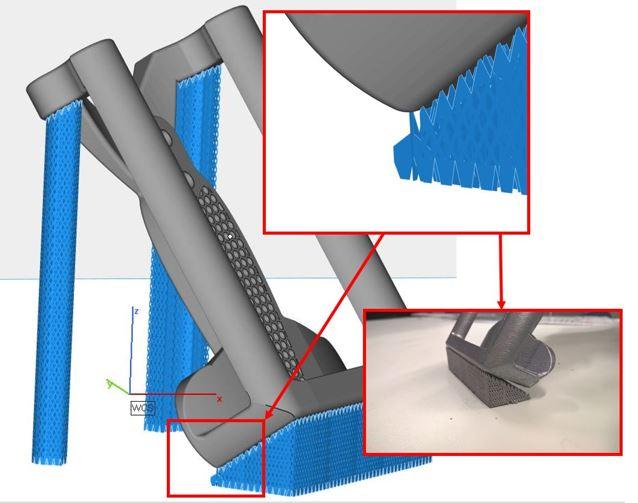
Jälkikäsittely ja lopullinen osa
Jälkikäsittelyyn sisältyi:
- alapinnan työstö (kiinnitys ja koneistus)
- kesto noin 5 min
- osan irrotus alustasta, yläpinnan tasoitus viilaamalla ja lasikuulapuhallus
- 20 min
Kuvassa 7 näkyy tulostettu osa jälkikäsittelyn jälkeen. Siitä nähdään poikkeamia rakenteessa; nämä johtuvat osittaisesta romahtamisesta skannauksen aikana. Etupuolen näkymä on sama kuin lopullisessa osassa.

Tulokset havainnollistuksen 1 versiolle 1
- Rakenne kestää kuormitukset
- Topologian optimoitu osa on noin 80 % kevyempi kuin massamalli. Lopullisen osan 1. version paino on mitattu massa- ja topologian optimoidulle mallille SolidWorksillä, ja 3D-tulostetun osan paino on mitattu Kernin FFN-vaa’alla. Tulokset on koottu taulukkoon 1.

- Tukirakenteita on paranneltava
- Kappaleen kokonaistilavuus on 0.033 dm3, josta tukien osuus on 0.005 dm3 à materiaalikustannukset yhdelle osalle ovat 100€ /kg * (0.033 dm3*2.7 kg/dm3) = 9 € / osa.
- Suunnittelun kesto oli noin 8 h
- Yhden osan tulostus kesti 8 tuntia ja 33 minuuttia, ja neljän osan 16 tuntia ja 30 minuuttia à vastaavat kustannukset ovat 660 € ja 1320 €
- 4 osan erässä kustannukset yhdelle osalle ovat 330 €
- Jälkikäsittely kesti 25 min/osa
versio 2
Version 1 tukirakenteessa oli ongelmia. Versiossa 2 tukirakenteita on paranneltu siten, että hammastukset tukirakenteesta on poistettu. Tämä tarkoittaa, että tukirakenne on eheämpi osan ja tukirakenteen rajapinnassa. Tämä tuki toimi hyvin tälle osalle. Taipumista ei tapahtunut, ja tukirakenteen ja osan rajapinta oli tiivis. Kuvassa 8 näkyvät version 2 tuet.

Havainnollistus 2; Osien yhdistäminen, monimutkaiset kanavat ja suutin
Tämä havainnollistus on suunniteltu kuvaamaan DFAM:n osien yhdistämismenetelmää, jossa liitetään useita osia yhdeksi kokoonpanoksi. Tässä havainnollistetaan onttoja rakenteita ja monimutkaisia kanavia. Osa on myös lohkottu niin, että ontot rakenteet voi nähdä.
Suunnittelu
Havainnollistuksessa on joitain olettamuksia:
- osa on materiaalin sekoittajan suutin, jossa
- on jäähdytys-/kuumennuskanava, joka kiertää sitä spiraalimaisesti
- kolme sisääntulokanavaa yhdistyneenä yhdeksi ulostulosuuttimeksi
- Materiaaliksi on valittu alumiini (AlSi10Mg), koska sen lämmönjohtavuus on hyvä
- Kahdeksan osaa on liitetty yhdeksi
- 4 jalkaa
- sisäsuutin
- keskirunko
- ulkorunko
- spiraalimainen kanavarakenne
Tämä osa oli havainnollistuskappale C3TS-projektissa.
Osa suunniteltiin niin, että tukia tarvitaan vain osan alapuolella. Uusi kerros tukee aina seuraavaa kerrosta. Osan suunnittelu kesti noin 12 h. Kuvassa 9 näkyy auki leikattu osa tukirakenteineen. Siitä voidaan nähdä kolme kanavaa, jotka yhdistyvät yhdeksi suutinrakenteeksi (ulostulo). Jäähdytys-/kuumennuskanavat kiertävät osaa spiraalimaisesti. Tukirakenteet, joita on vain osan alapuolella, on merkitty sinisellä.

3D-tulostus
Osa 3D-tulostettiin 30 µm kerrospaksuudella, koska kanavien pinnanlaadun täytyi olla hyväksyttävällä tasolla. Osa tulostettiin siten, että tukirakenteet ovat vain osan alapuolella. Kaikki tuet ovat tasaisilla pinnoilla, joten ne on helppo työstää pois. Tuet kiinnitetään osaan, eikä osan ja tukirakenteen rajapinnassa tarvita hammastusta. Osan kokonaistilavuus on 0.09 dm3, josta tuen osuus on 0.002 dm3. Materiaalikustannukset ovat siten 24.3 € /osa (0.09 dm3*2.7 kg/dm3*100 €/kg). Tulostusaika yhdelle osalle on 11 tuntia ja neljälle osalle 29 tuntia, joten kustannukset ovat noin 880 € (80 €/tunti * 11 tuntia) ja 2320 € (80 €/tunti * 29 tuntia). Neljän osan erässä yhden osan kustannukset ovat 2320€/4 = 580 €. Tulostettu osa näkyy kuvassa 10.
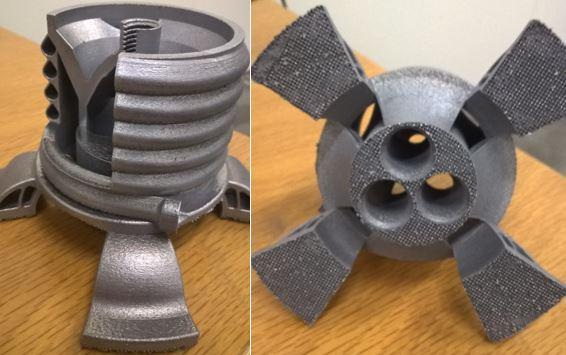
Jälkikäsittely
Jälkikäsittelyyn sisältyi:
- osan irrottaminen alustasta
- aika/osa 5 min
- koneistus
- aika/osa 20 min
- lasikuulapuhallus
- aika/osa 5 min
Jälkikäsittelyn kesto yhteensä osaa kohti on 30 min.
Tulokset havainnollistukselle 2
- Rakenne saatiin onnistuneesti tulostettua ensimmäisellä kerralla
- Kahdeksan osaa yhdistettiin yhdeksi
- Tukirakenteita optimoitiin niin, että 2.2 % kokonaistilavuudesta on tukirakennetta
- Tulostusaika 1 osalle on 11 tuntia ja kustannukset 880 €
- Tulostusaika 4 osan erälle on 29 tuntia ja kustannukset yhtä osaa kohti 580 €
- Jälkikäsittelyn kesto on noin 30 minuuttia
- Suunnittelun kesto oli noin 12 tuntia
Viitteet
/1/ Swain A.K National Pragramme on Technology Enhanced Learning, Introduction to DFMA. https://nptel.ac.in/courses/107103012/module1/lec1.pdf [18.4.2019]